- April 28, 2023
- Posted by: Muhammad Shoaib Afzal
- Category: IV. Production Module
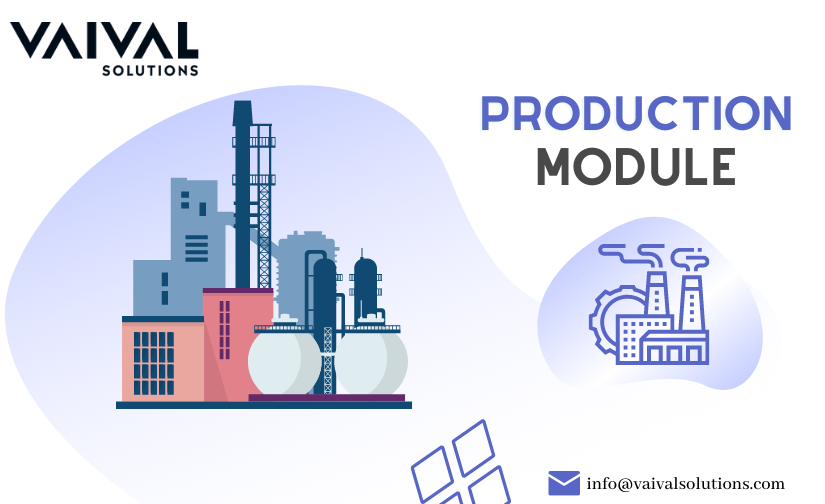
PRODUCTION MODULE
Vaival ERP system helps in material planning and control. It enables managers to plan and track the use of raw materials, components, and finished goods throughout the production process. This helps in ensuring that the right materials are available at the right time, and in the right quantity, minimizing inventory levels and reducing waste. It also helps in production monitoring. It enables managers to monitor the progress of the production process in real-time, and to identify and address bottlenecks or issues that may arise. This assists in ensuring that production is executed efficiently and effectively, with minimal delays or interruptions. Overall, our ERP system allows you to streamline the production process, reduce waste, and improve productivity and efficiency, leading to increased profitability and customer satisfaction.
SETTING UP INVENTORY:
The first step in the production module is to add the relevant components of the inventory i.e., Raw Material and Finished Goods. To learn how to add inventory please read our blog on Business Setup, that will guide you on how you can add inventory into the system. After providing a system with all the necessary components of your inventory i.e., raw material, semi-finished goods, finished goods and conversion or variety of packing size if necessary, depending upon the nature of your business you can use the Production Module.
1- ADD SEMI FINISHED GOODS:
A semi-finished item is an intermediate product that has gone through some stages of the production process but is not yet a finished product. It may require further processing, assembly, or modification before it can be sold or used in other products. In this screen you will add Semi-Finished Goods to produce Finished Goods which means that you will be adding many raw materials or semi-finished goods to produce one product.
Figure: Production Module > Add Semi Finished Item
Now to add Semi-Finished goods you have to click on “Add Semi-Finished Good”. As you click on the button a pop-up will open, and it will ask you to add, Production Item Name, which means, what is being produced by using the below stated materials. And then the Production Quantity of production item, production quantity meaning how much of this item is being produced by using this quantity of raw material or semi-finished goods. In the fields below Recipe Item Name, Recipe QTY and Recipe Unit, you have to enter the raw materials or semi-finished goods used to produce the above stated Production Item Name. You can always add more by clicking on the green “PLUS SIGN” to add more materials to your recipe. And after providing the details you need to click on “SAVE”. You can always come back to this screen to edit the recipes.
Figure: Production Module > Add Semi Finished Item 2
2- DIRECT BATCH PROCESSING (RMS):
In this screen you have to tell the system that, what will be the site of the Production item, that is being produced, batch date, third party if any. Then you will select the Production item that you are producing. When you select a Production item that you produced in the earlier screen, the system will automatically fetch the Production Unit and Production QTY of the selected item, and then you need to provide Batch QTY and Produced QTY. The system will automatically reduce and consume the inventory while performing this process as you have entered the actual produced quantity of the underlying Produced Item in this screen. This screen is also used by the names, Bill of Materials (BOM) or Bill of Quantity (BOQ) or recipe depending upon the nature of the business.
Figure: Production Module > Direct Batch Processing
A- Draft Listing
This screen allows you to view, add notes, attach files, update consume quantity, and update batch quantity. You can also delete your draft Produced Quantities by clicking the checkbox, as you click on the check box system will ask you whether you want to Approve or Delete the selected entry. Using the filters (Site Name, Transaction Type, Date From/To, Voucher No., and Prepared by) you can find the saved entries in the system. Also, you can choose to view the draft entries of a whole financial year from the Financial Year filter. A draft that is canceled is deleted from the system. Approved drafts appear in the Approved Listing as record.
Figure: Production Module > Direct Batch Processing > Draft Listing
B- Approved Listing:
All the data after approval from the draft listing goes in the approved listing and only this data is recorded.
Figure: Production Module > Direct Batch Processing > Approve Listing
3-STOCK CONVERSION:
Stock conversion is the process of converting one type of stock into another. This can involve changing the unit of measure, the form of the product, or the packaging.
In our system this stock conversion feature operates the same. Once you have made all of your produced items in the previous screen, you can convert them here as different types of packing etc. You need to enter the “Stock Item Name” that you want to pack etc. and the system will automatically fetch Stock Unit, Quantity and Base Unit Quantity. Now the system will ask what you want to convert this item into. If you are using this screen, you must open these inventory types before from the business setup module and to learn how to add inventory you can visit our “Business Setup Blog”. Now you will provide the inventory to the system into which you want your Stock Item Name to be converted. E.g., you produced potato chips and here you want to pack them in the packaging of PKR. 50/- PKR. 100/- PKR.200/- so you will select the packing names and the system will automatically fetch the relevant quantities of these packings. After providing the necessary details click “SAVE AS DRAFT”.
Figure: Production Module > Stock Conversion
STOCK ASSEMBLE VOUCHER, this voucher refers to the process of creating a finished good by combining different components. If you don’t manufacture or produce inventory and just assemble the inventory, you will use this screen from our system to convert different products to produce one product.
A- Draft Listing (Stock Conversion / Stock Assemble Voucher):
This screen allows you to Edit, Preview and Export, Add Note, and Add Attachment. You can also delete your draft Produced Quantities by clicking the checkbox, as you click on the check box the system will ask you whether you want to Approve or Delete the selected entry. Using the filters (Site Name, Transaction Type, Date From/To, Voucher No., and Prepared by) you can find the saved entries in the system. Also, you can choose to view the draft entries of a whole financial year from the Financial Year filter. A draft that is canceled is deleted from the system. Approved drafts appear in the Approved Listing as record.
Figure: Production Module > Stock Conversion/Stock Assemble Voucher > Draft Listing
B- Approved Listing (Stock Conversion / Stock Assemble Voucher):
All the data after approval from the draft listing goes in the approved listing and only this data is recorded.
Figure: Production Module > Stock Conversion/Stock Assemble Voucher > Approve Listing